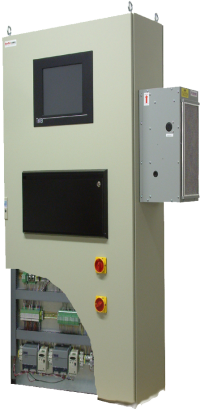
We use both the 1000 System and the 500 System as upgrade platforms, depending on the type and complexity of the older gauge system. Benefits to upgrading older gauge systems to the SenTek 1000 or 500 include:
Cost Savings: With a low component count and commercially available components, our platform products are inexpensive to purchase and especially to maintain. In some cases the purchase cost of a new upgrade system is equal to or lower than the cost to replace even one proprietary component in an older gauge system.
Flexible setup: With an open architecture and LabVIEW software, each upgrade system can be expanded and customized with little effort. Special operator screens and host link interfaces are easily added or changed.
Improved Performance: SenTek’s high-speed signal processing results in faster measurement and considerably lower sensor noise. Combined with our new Electrometer we can tune older gauge devices to meet new requirements without costly gauge replacements.
Fast Installation/Conversion: The simple architecture of the new gauge platforms permits us to convert and install the upgrade components in some cases as quickly as a day, resulting in very little downtime on the machines.
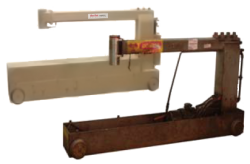
Gauge rebuilds
Our new sensor components are in most cases much smaller than those of older gauge devices. This allows us to install new sensor components in older gauge frames. We have successfully rebuilt many decades-old C-frames and O-frames resulting in new high-speed measurement without any changes to the mill mechanics.
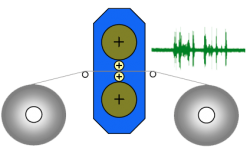
Higher frequency vibration harmonics resulting from undesired interaction between the work rolls and backup rolls can cause very narrow but significant thickness variations in the rolled product. These thickness variations are often too narrow for conventional thickness gauges to detect and report. Over the past several years, SenTek has developed a set of tools and techniques for detecting, reporting and analyzing these thickness variations.
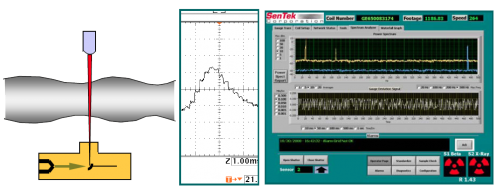
In a modern, high-speed rolling mill, the gauge and the mill control form a large feedback loop that can make it very difficult to determine whether the gauge device is accurately measuring the thickness variations. Our very high speed X-ray gauge with a micro-focus beam combined with a spectrum analyzer built in to the gauge device will detect and report even very narrow bands of thickness variations. A heavy-duty accelerometer in the gauge device will display the vibration frequencies and allow the user to determine which frequencies are due to actual thickness variations, roll eccentricity problems, and those that are due to vibration. These tools are available as part of our gauge systems or as stand-alone rolling mill tools and services.